Des changements de production SMED pour Sérénité, Maîtrise, Efficience et respect des Délais !
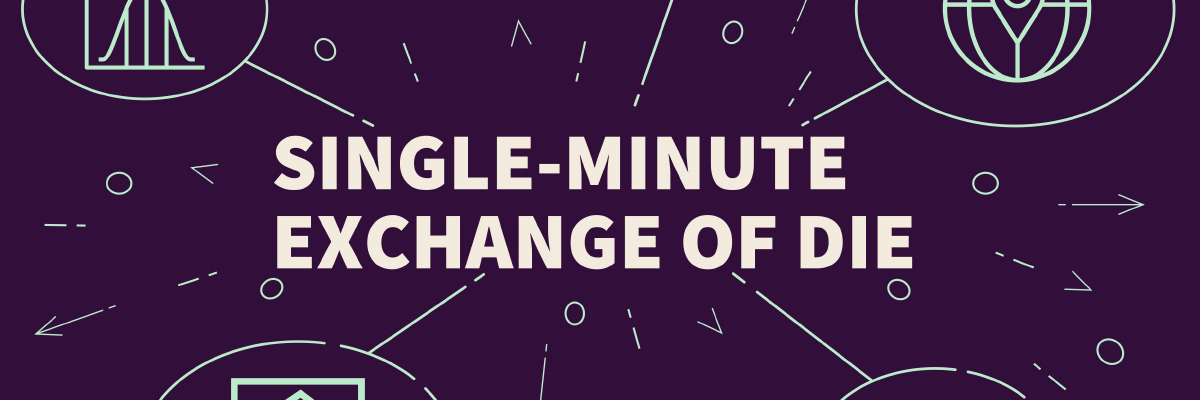
La phase qui sépare deux productions successives est un vrai révélateur. Quand le domaine le permet encore, sa planification peut donner lieu à de véritables bras de fer : d’un côté la production qui souhaite les limiter, chaque changement étant une lourde perte de temps et de matière, de l’autre la centrale planning qui voit dans l’allongement des séries, des clients non satisfaits et un taux de service qui s’écroule. Pour d’autres dont le marché impose déjà des séries de plus en plus courtes et une plus grande diversité de produits, l’efficience et le respect des délais deviennent un enjeu décisif pour l’entreprise.
Sur le terrain la mise en œuvre s’avère délicate. Pour les opérateurs, c’est un moment de tension qui donne lieu, dans la précipitation, à des comportements à la limite de leur sécurité pour ne pas dire dangereux. Changer de série rend ainsi visible les problématiques du type dérives d’état standard, absence de standards, de formation ou d’autonomie. Sur des machines ou process complexes, il révèle également des difficultés de synchronisation entre opérateurs et services.
Le SMED (Single Minute Exchange of Die) apparaît dans ces conditions comme un moyen de réconcilier les attentes de chaque partie prenante. Toute la puissance de la démarche se trouve dans son aspect participatif. Au travers de groupes de travail opérationnels et pluridisciplinaires, cet outil du Lean s’attache à :
- Analyser les données existantes. Facultatif mais riche en informations, un premier passage de ces données aux outils statistiques du 6 Sigma peut s’avérer judicieux. L’avantage sera de mettre le doigt sur les facteurs les plus influents et donner une idée de leur impact sur les temps de changements.
- Identifier les opérations internes réalisables uniquement pendant l’arrêt et les opérations externes réalisables machine en fonctionnement.
- Décaler les opérations externes en amont ou en aval du changement pour les réaliser en « temps masqué » durant la production.
- Réduire les durées des opérations internes dans un premier temps puis des opérations externes. Faire l’impasse sur cette dernière action laisserait supposer que les équipes ne sont pas déjà chargées durant les temps de fonctionnement.
Pour ce faire, l’appel à l’observation chronométrée voire à la vidéo va s’avérer nécessaire. Cette phase peut faire naître craintes et appréhensions. Une communication auprès du personnel et de leurs représentants est donc la bienvenue pour ne pas biaiser l’observation qui se doit d’être au plus près de la réalité. L’objectif est bien de diminuer l’impact des changements de production en pensant avant tout aux acteurs de cette opération. Ce sont eux qui, au travers de l’équipe projet, vont proposer et tester des solutions souvent simples, d’ordre organisationnelles ou techniques, en vue de supprimer les tâches à non-valeur ajoutée ou les réduire le cas échéant.
La flexibilité et la réactivité obtenues par les gains en temps et pertes au démarrage procurent une véritable agilité et un avantage concurrentiel certain. S’ouvrent aussi les portes des petites séries synonymes de maîtrise des stocks et de nouveaux marchés inaccessibles jusqu’alors. Mais encore faudra-t-il pérenniser la démarche ! L’accompagnement des équipes opérationnelles et managériales va s’avérer primordial. La formation au standard et à son respect, l’idée qu’il n’est pas figé et sera optimisé à l’apport de nouvelles idées et solutions permettra une appropriation de la méthode.
Il aura fallu presque 30 ans à la F1 pour passer d’un arrêt au stand de plusieurs dizaines à une poignée de secondes. L’idée est de commencer et se lancer le défi de ne plus s’arrêter.