Les outils de base | Partie 2 : Les fondations d’une démarche Lean Management
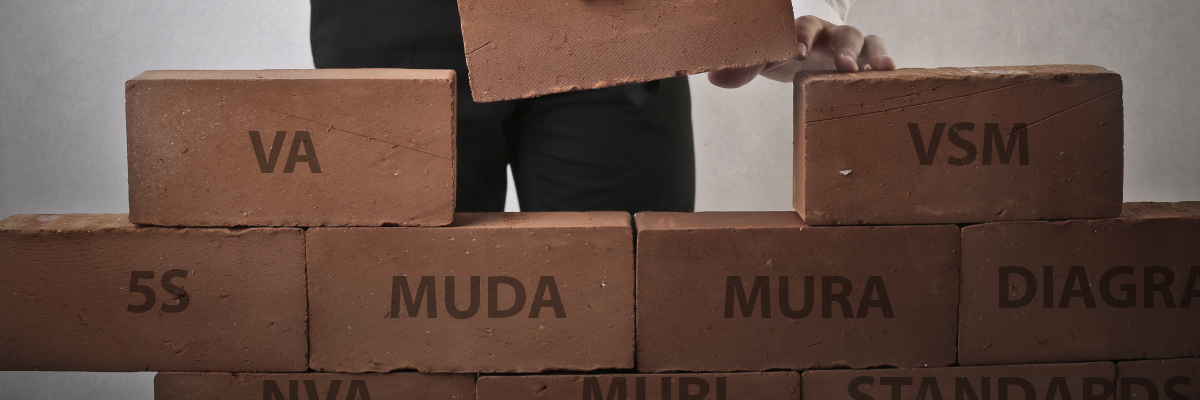
Dans la première partie de cette série d'articles, je vous ai rappelé les fondements d'une démarche de "Lean Management". Cette remise au clair permet maintenant de rentrer dans le vive du sujet en abordant notamment les outils piliers de cette démarche Lean.
1. VA / NVA
Comprendre la notion de Valeur Ajoutée (VA) est fondamental puisque que par défaut, ce qui n’est pas de la VA est du gaspillage, de la Non Valeur Ajoutée (NVA).
Dans la définition que nous adoptons, la VA est ce que le client est prêt à payer pour obtenir la satisfaction de son besoin.
Concernant la NVA, nous considèrerons deux types de situation :
- La NVA 100% inutile que nous devons éliminer
- La NVA nécessaire qui est indispensable pour pouvoir réaliser la VA mais que nous devons réduire.
Nous trouverons par exemple les opérations de préparations, de réglages, de maintenance qui ne sont pas de la VA mais qui sont bien nécessaires à nos processus pour accomplir les opérations de VA.
2. MUDA, MURA, MURI : Les 3 nuisibles
Définir et identifier sur le terrain ce qui est nuisible pour nos processus nous permettra de construire les bases de notre système d’amélioration.
Les nuisibles sont différenciés en trois grandes familles.
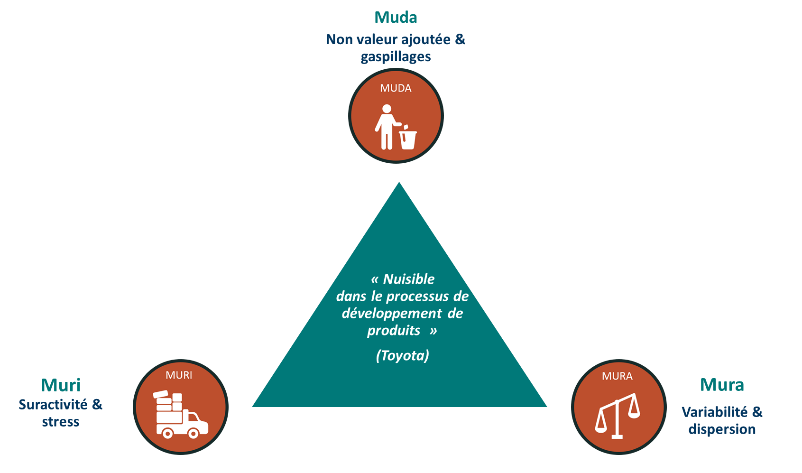
Plus ces nuisibles sont présents dans les processus, plus il est probable que les stocks et contrôles soient importants. Les stocks sont alors utilisés comme absorbeurs des différentes instabilités provoquées par les nuisibles.
- Les Mura : Tout ce qui est erratique, irrégulier avec de la variabilité et de la dispersion
- Les Muri : Tout ce qui concerne la suractivité qui va mettre en tension le personnel, l’organisation et les équipements
- Les Muda : Le 7+1 gaspillages qui sont ou qui génèrent de la NVA
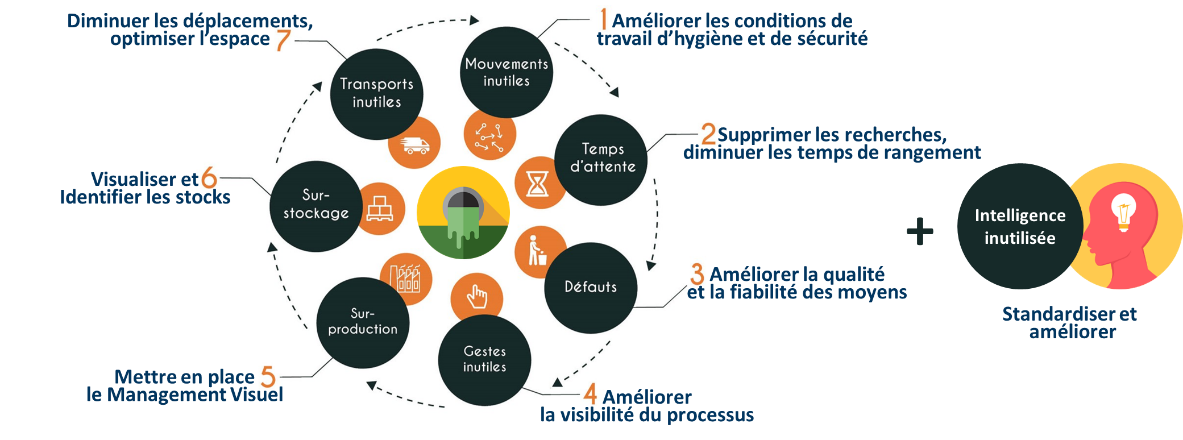
Si les Muda sont réduis, si les Mura sont maitrisés, alors il y aura moins de Muri et il sera possible de travailler en flux tirés tout en baissant les stocks ! CQFD !
Voir nos articles sur les gaspillages et la maîtrise de la variabilité
3. La VSM (Value Stream Mapping)
La cartographie de la valeur ou VSM est un outil essentiel pour comprendre et partager la vision du fonctionnement d’un processus de production. LA VSM est réalisée sur la base des données réelles collectées sur le terrain. Pour chaque opération sont collectés les Indicateurs de performance du processus (IPP) tels que le temps de cycle, le taux de rendement synthétique (TRS), le taux de bon du 1er coup, le taux de rebuts et le niveau d’encours entre chaque opération. La VSM est réalisée collectivement par les acteurs du processus. La VSM a pour objectifs les points suivants :
- Discriminer les tâches à VA et NVA
- Partager une même représentation des activités du flux et des pertes d'efficience
- Visualiser les potentiels d’amélioration
- Réduire les délais et supprimer des gaspillages
- Définir les chantiers à mener
Identifier les points à améliorer à partir de la cartographie actuelle permet d’établir une feuille de route pour atteindre le flux cible.
4. Le diagramme de flux
A l’instar de la VSM, le diagramme de flux permet essentiellement de cartographier les flux des processus transversaux et administratifs.
L’ensemble des acteurs sont tout d’abord identifiés puis intégrés dans le diagramme en fonction de leur ordre d’apparition. A chaque acteur correspond une ligne. Les actions de chaque acteur sont inscrites chronologiquement sur la ligne correspondante. A chaque changement d’acteur correspond un changement de ligne.
Le diagramme de flux permet ainsi de visualiser quand un processus est trop dépendant d’une ressource, quand il y a des doubles saisies ou autres opérations de NVA.
Tout comme pour la VSM, le diagramme de flux permet d’identifier les points à améliorer à partir de la cartographie actuelle et permet d’établir une feuille de route pour atteindre le flux cible.
5. Les 5S
Les principes des 5S sont simples et plein de bon sens. Si l’on met aussi souvent en avant la pratique de cette méthode, c’est qu’elle est fondamentale dans le processus d’amélioration continue. Sa bonne application constitue d’une certaine façon un « stress test » de l’organisation.
Étape 1 – Supprimer en triant l’utile de l’inutile
Étape 2 – Ranger en trouvant une place pour chaque chose
Étape 3 – Nettoyer et remettre en état
Étape 4 – Standardiser la bonne pratique choisie par les utilisateurs du poste
Étape 5 – Pérenniser en s’assurant du respect des standards
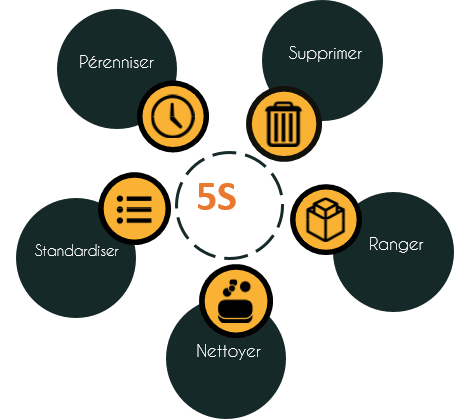
Les étapes Eliminer et Ranger contribuent à l’amélioration de la sécurité et de la sérénité sur le poste de travail, l’étape Nettoyer/Remettre est la première étape dans la mise en œuvre de l’auto-maintenance des équipements, l’étape Standardiser contribue à formaliser les meilleures pratiques. Enfin l’étape Pérenniser contribue à renforcer le système de management.
6. Les standards
« Sans standard, pas de Kaïzen ! » Taiichi Ohno, père du Toyota Production System (TPS)
Le standard est la représentation de la meilleure pratique du moment. La référence.
Le sens de la citation de Taïchi Ohno est que s’il n’y pas de standard, il n’y pas de bonne pratique à laquelle se référer pour s’en servir de point zéro à toute amélioration.
Le standard formalisé, vérifié comme étant applicable et appliqué sur le terrain, permet de réduire la variabilité des processus.
Le standard est la référence pour former les nouveaux utilisateurs d’un poste de travail ou encore l’ensemble des utilisateurs lorsqu’il y a une modification des pratiques. Il sert de support pour le formateur et le nouveau formé peut s’y référer jusqu’à ce qu’il ait acquis le savoir-faire suffisant.
Voir nos articles sur les standards et les chantiers d'amélioration.