Combiner efficacité et efficience opérationnelle
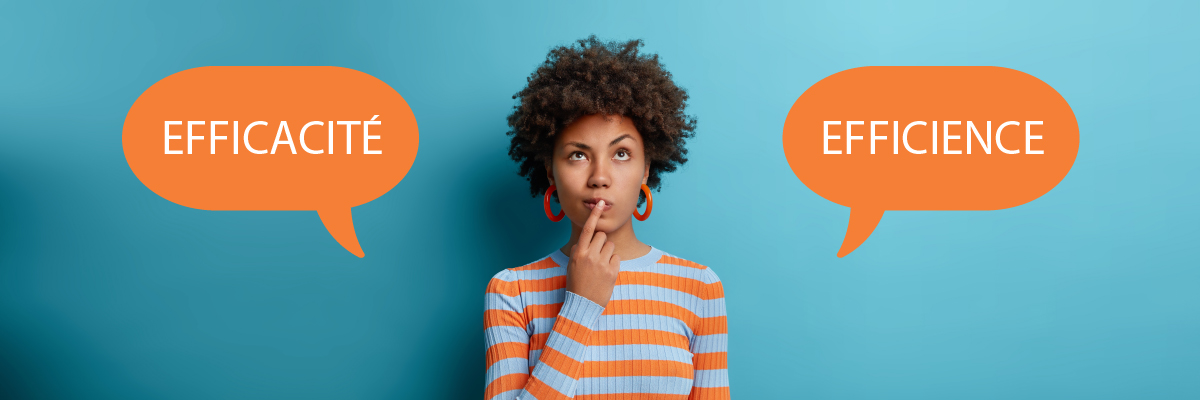
Efficacité et efficience sont des termes régulièrement employés dans les entreprises, souvent sans réellement distinguer la différence entre les deux. Pourtant, pour être performante, une entreprise a besoin de chacune de ces deux notions.
Pour mettre en lumière les différences entre les deux termes, on peut résumer leurs définitions respectives par les expressions suivantes :
- L’efficacité consiste à atteindre l’objectif.
- L’efficience consiste à consommer le juste nécessaire de ressources pour parvenir à l’objectif.
Dans les entreprises, et dans celles de production en particulier, efficacité et efficience des différents flux sont toutes deux importantes et correspondent à des séquences de pilotage managériales différentes.
L’efficacité consistant à atteindre l’objectif, il est donc essentiel de commencer par bien déterminer celui-ci. En d’autres termes, l’efficacité dépend en premier lieu du choix de la cible à atteindre.
L’application de principes du Lean Management permet de connecter efficacité et efficience.
Les objectifs au service de l’efficacité
Une démarche Lean globale commence par clarifier les objectifs stratégiques de l’entreprise puis à les décliner en objectifs opérationnels temporellement priorisés. La priorisation permet de gérer la charge/capacité des ressources humaines en les focalisant sur les bons sujets avec le bon timing.
Mettre en œuvre une démarche Hoshin Kanri permet de clarifier la stratégie moyen terme, pour la décliner en objectifs opérationnels annuels qui sont eux-mêmes servis par des chantiers d’améliorations priorisés.
Les objectifs sont ainsi connectés aux enjeux et les équipes peuvent se concentrer sur l’amélioration des flux internes les plus importants.
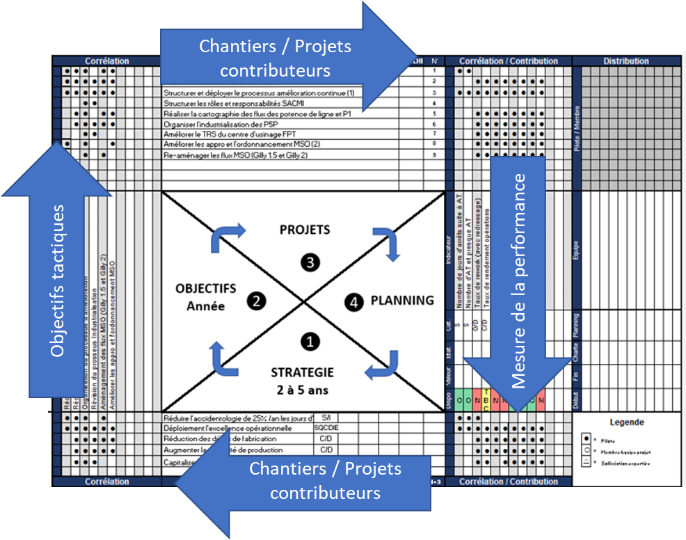
Exemple d’approche Hoshin Kanri.
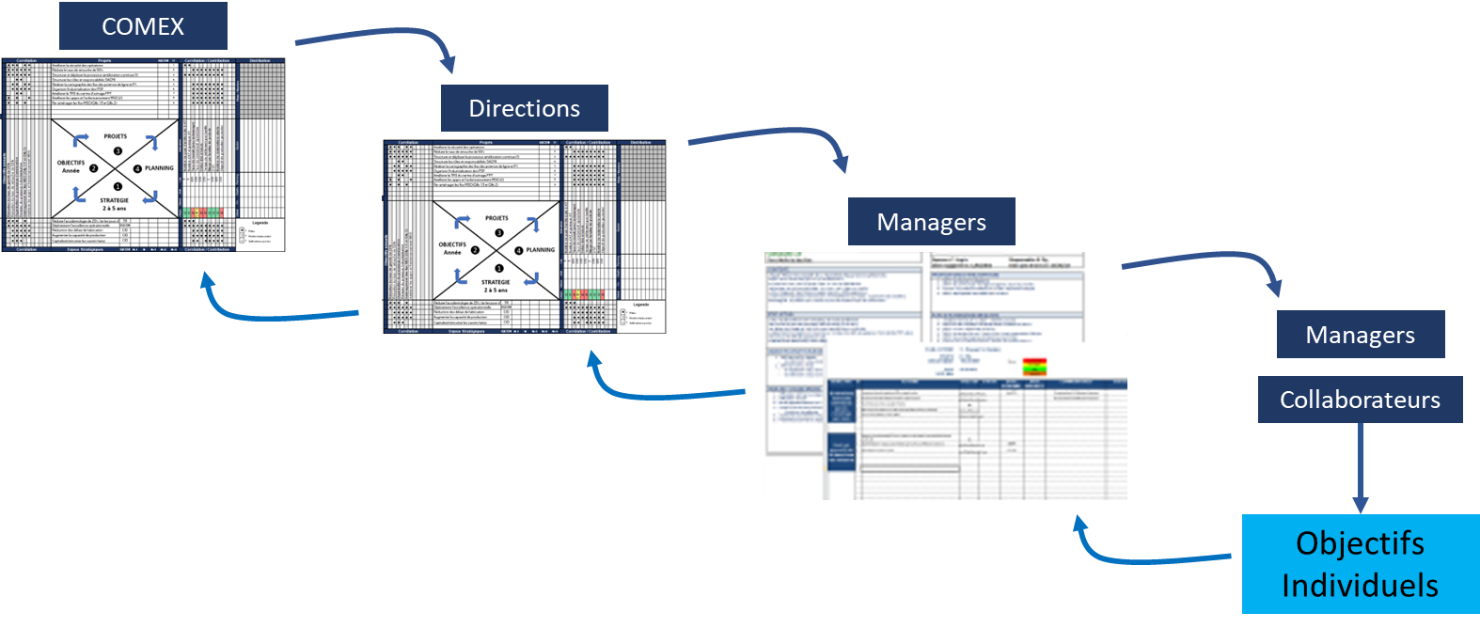
Déclinaison des objectifs (cascading) jusqu’aux chartes projets des différents chantiers d’amélioration.
Améliorer les performances en améliorant l’efficience des flux
L’enjeu est de produire puis de livrer au client le bon produit, au bon endroit, au bon destinataire, dans les délais convenus avec le juste nécessaire de ressources : ressources en moyens de production (taux d’utilisation des équipements), en matières et composants (réduction des pertes matières et des produits non conformes) et en main d’œuvre (temps de préparation, temps de réglage, temps de production, temps de contrôle).
Cartographier les flux les plus importants pour la stratégie de l’entreprise va nous permettre de caractériser leur efficience et d’identifier ce qui les pénalise.
Réaliser une VSM (Value Stream Mapping) sur le flux de production le plus stratégique permet de matérialiser le flux réel observé sur le terrain en collectant les données permettant de mesurer sa performance (% de rebuts, temps de cycle effectif, temps de réglage effectif, fiabilité…) tout en collectant les irritants des collaborateurs qui conduisent les opérations au quotidien (micro défaillances, disponibilité des outillages, qualité des outillages, difficultés de réglages…).
Cette recherche des différentes causes de perte d’efficience par l’identification des gaspillages et des opérations sans valeur ajoutée, va permettre d’identifier les opportunités d’améliorations en les priorisant en fonction de leur difficulté de mise en œuvre et de leur impact sur le flux (matrice impact/effort).
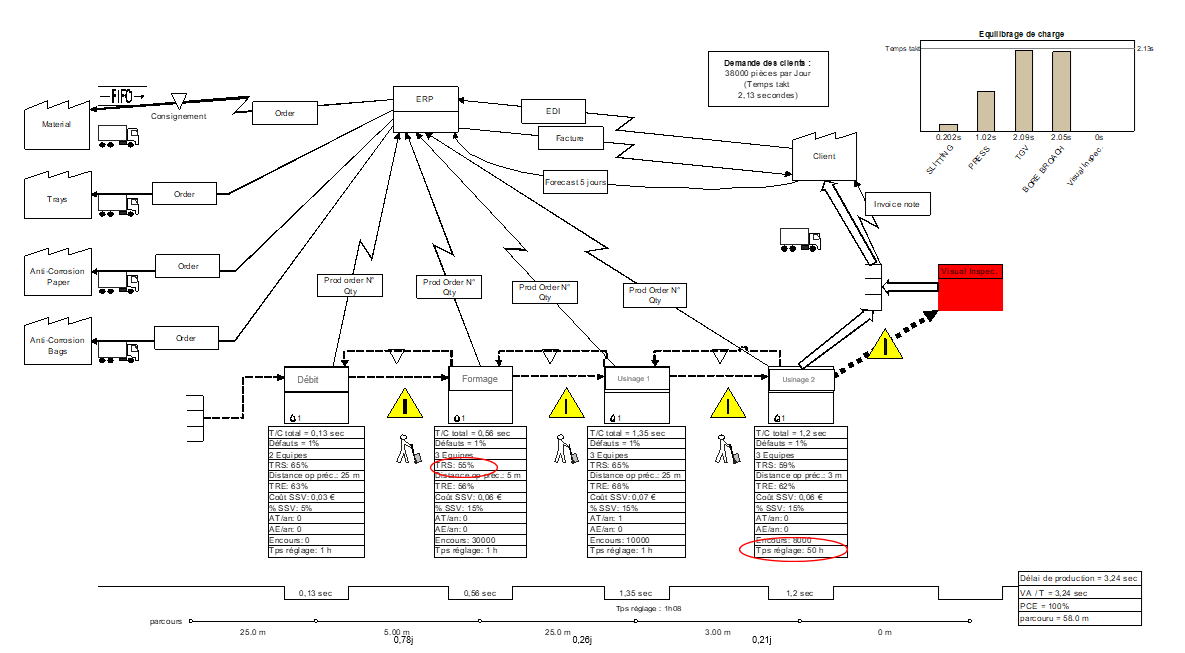
Exemple de VSM.
En complément de la VSM, la réalisation d’un diagramme Spaghetti, en accompagnant les collaborateurs sur le terrain, permet d’identifier les gaspillages et risques lors des cheminements physiques des personnes et des composants.
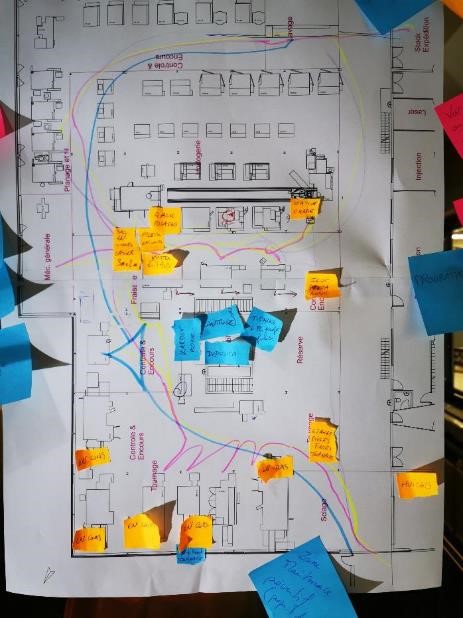
Exemple de diagramme Spaghetti.
Un flux de production est dépendant de flux transverses qui viennent l’alimenter en matières, moyens, compétences ou informations.
L’amélioration de l’efficience est une démarche transversale dont le bénéficiaire est le flux en faisant en sorte de l’accélérer. Les phases de préparation de la production (plan industriel et commercial, industrialisation, nomenclature, gammes, approvisionnements matières et outillages) sont tout aussi importantes que la production elle-même.
La cartographie de ces flux transverses permettra d’identifier de nouvelles opportunités d’améliorations qui seront bénéfiques à l’ensemble de l’organisation (flux transverses et flux de production).
Réaliser un diagramme de flux permet de matérialiser le flux en identifiant les tâches réalisées par chacun des acteurs. Les interactions entre acteurs sont visibles et permettent d’identifier les situations qui viennent ralentir le flux (tâches sans valeur ajoutée pour l’activité, validations multiples, …). A l’identique de ce qui est pratiqué lors d’une VSM, les irritants des collaborateurs sont collectés (données incomplètes, erronées, saisies multiples, …).
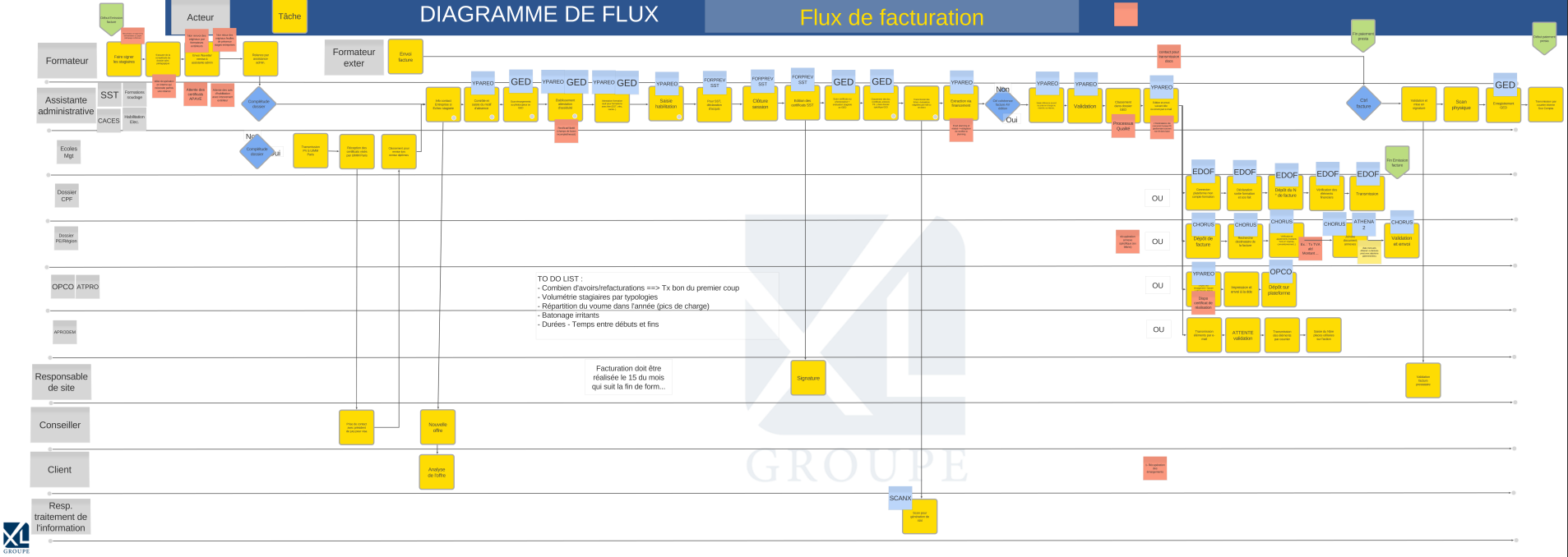
Exemple de diagramme de flux administratif.
Calculer l’efficience globale du flux
Cartographier les flux permet d’identifier les causes de perte d’efficience et d’en mesurer l’impact sur le flux.
L’efficience est calculée sur la base des données de temps collectées lors de la cartographie du flux.
- Le LEAD-TIME : temps de déroulement du processus (temps vu par le client entre le moment où il passe sa commande et le moment où il est livré).
- Temps à VA : temps passé à la création de valeur.
- Temps à NVA : temps passé sans création de valeur pour l’activité (attentes, non qualité, …).
Le ratio d'EFFICIENCE FLUX = Part du temps consacrée à la VA = Temps VA / Lead Time
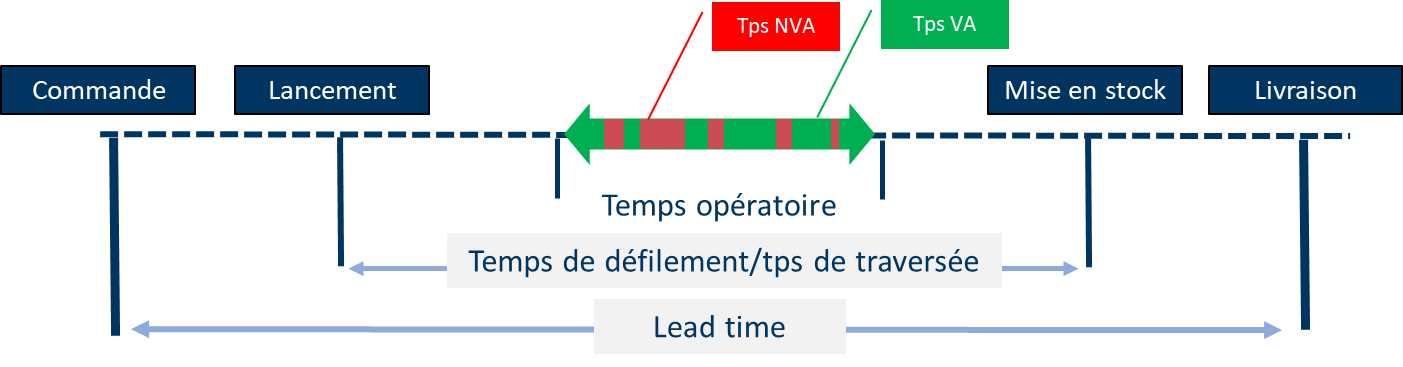
Les bénéfices de la recherche de l’efficience
Améliorer l’efficience consiste à accélérer le flux en identifiant puis en réduisant les gaspillages de tous les flux industriels.
Les bénéfices sont mesurables sur les 4 axes de performance (Sécurité/Sérénité, Qualité, Délais, Coûts).
- Sécurité/Sérénité : Si les collaborateurs travaillent avec moins d’irritants quotidiens, parce que ceux-ci auront été captés puis traités, il en découlera une spirale vertueuse permettant de développer la culture de l’amélioration continue. Cela contribue à l’amélioration des conditions de travail et augmente l’attractivité de l’entreprise.
- Qualité : Il n’y a aucun sens à accélérer un processus défectueux ! Travailler sur la réduction de la non-qualité pour tendre vers le bon du premier coup (jidoka) permettra de réduire les réclamations clients, de réduire les coûts induits et d’accélérer le flux en évitant le retravail nécessaire pour compenser les rebuts, les tris ou les retouches.
- Délais : Accélérer le flux permet de réduire le lead time entre commande et livraison. Le délai perçu par le client peut donc être diminué pour devenir un facteur différenciant par rapport à la concurrence.
- Coûts : Les ressources étant mieux utilisées et les gaspillages diminués, les coûts variables sont réduits en conséquence. Un flux mieux maitrisé permet de réduire les encours et donc les niveaux de stocks au bénéfice de la trésorerie. La capacité dégagée par la meilleure utilisation des équipements, permet soit de diminuer les coûts en réduisant les transports exceptionnels et les heures supplémentaires, soit de récupérer de la capacité de ventes permettant d’amortir les coûts fixes.
Les facteurs clés de succès pour améliorer l’efficience des processus
- Disposer d’une stratégie de développement claire afin d’aligner le plan d’amélioration et travailler sur les flux les plus pertinents.
- Impliquer tous les acteurs de terrain (ceux qui réalisent) et les sponsors. Cette approche permettra d’intéresser les acteurs aux enjeux et de les impliquer dans la mise en œuvre d’une vision partagée.
- Planifier les chantiers et anticiper les besoins de libération de ressources (équipements, équipes, prestataires).
- Organiser les agendas des équipes pour réaliser, tester, mettre au point et valider les solutions.
- Prévoir un budget « amélioration » pour ne pas bloquer certaines opportunités non budgétées.
Pour en savoir plus sur ce sujet, je vous invite à visionner le replay de la web-conférence « Performance Industrielle : Rendre efficients vos flux de production avec le Lean Manufacturing ».