Les outils de base | Partie 3 : Le juste à temps et les flux tirés
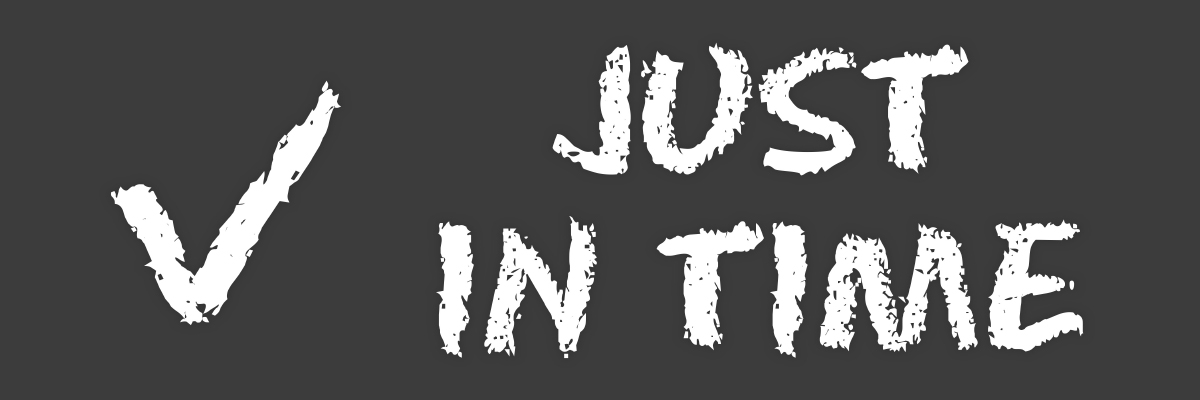
Avec le Jidoka (la conformité), le juste à temps (JAT) est l’un des deux piliers du Lean.
Le principe général est simple : produire seulement en fonction de la demande client et livrer au client le bon produit, au bon moment, avec la juste quantité demandée.
Nous entrons donc dans la logique de flux tiré que nous opposons à la logique de flux poussé qui consiste à produire sans s’assurer qu’il y a bien consommation des stocks.
Quand le flux est tiré par la demande, tout est organisé en fonction de la consommation. Depuis les approvisionnements de matières premières et composants jusqu’à la production, opération par opération.
Pour éviter les ruptures de flux et réagir rapidement à la demande, des buffers ou stocks tampons sont positionnés en des points stratégiques. Ces stocks sont maitrisés et contrôlés par des systèmes de pilotage visuels entre poste tels que le système kanban.
JAT ne signifie pas stock zéro !
Pas de demande = pas d’approvisionnements = pas de production = pas de production de stock !
Le flux est tiré par la demande ! CQFD !
Le principe général du flux poussé n’est acceptable que lorsque la demande est supérieure à la capacité de production…sous réserve que la capacité de production de chaque poste du processus soit globalement équilibrée.
Le principe du JAT s’applique à l’intégralité des processus d’approvisionnement, de production et de stockage.
Contrairement à de nombreuses interprétations, le JAT ne signifie pas stock zéro. Un fonctionnement à stock zéro serait synonyme de fragilité extrême en cas de variation de quelque origine que ce soit.
Le JAT fonctionne avec des stocks réduits et contrôlés. Le fait de fonctionner avec des stocks réduits nécessite de réduire les nuisibles tout au long du processus. Une entreprise organisée en JAT est agile.
La gestion de la demande, la planification, l’ordonnancement et les approvisionnements doivent être synchronisés et pilotés de manière collaborative et visuelle dans un environnement permettant de fonctionner sur la réalité de l’activité et non sur des hypothèses.
Pour autant, il ne s’agit pas d’opposer les différents modes de production. En effet, dans certains cas (produits en lancement, …), la logique de planification en mode poussé peut tout à fait convenir et permettre d’anticiper des volumes de vente prévisionnels non stables et non connus. Il est également tout à fait possible de combiner une approche « flux poussé » afin d’identifier les volumes d’achats prévisionnels (cas des MP à long délais) et une approche « flux tiré » permettant de déclencher la production sur la base de la consommation moyenne journalière (CMJ).
Voir nos articles sur les flux tirés et le DDMRP
Pour déployer une organisation en JAT, il est indispensable de travailler sur plusieurs éléments du système de production :
1. Produire suivant le Takt-Time tout au long de la chaîne de valeur
Takt signifie métronome. Le Takt-Time donne la cadence que doit avoir le processus pour répondre à la demande du client en fonction du temps disponible pour la production.
Le Takt-time donne le temps unitaire cible de réalisation de chaque pièce. Il permet de définir l’organisation cible qui permettra de répondre au besoin client en ne produisant que le juste nécessaire.
Takt-Time = Temps disponible / demande client
Exemple :
Un atelier de production fonctionne en 1 équipe de 7h à raison de 5 jours par semaine, soit 2100 minutes par semaine.
Chaque semaine le client commande 350 articles d’une même famille.
Takt-Time = 2100 minutes / 350 articles = 6 mn /article
Connaître le Takt-time permet de s’assurer que chaque opération est capacitaire pour produire au rythme de la demande client. Le but ultime étant d’équilibrer les postes pour que chacun produise le plus possible au même rythme. Produire conformément au Takt-Time ne signifie pas produire exactement au Takt-Time. Dans ce cas de figure nous serions exposés aux moindres aléas du processus. Il est recommandé de conserver une marge capacitaire de l’ordre de 20%. Cette marge sera plus ou moins importante en fonction de la robustesse éprouvée du processus.
2. Réduire les tailles de lots en réduisant les temps de changements de séries
Réduire les tailles permet de réagir rapidement aux différentes demandes sans générer de stocks tout en accélérant le temps de traversée du processus. Réduire la taille des lots nécessite d’être capable de réduire les temps de changements de séries en déployant la méthodologie SMED (Single Minute Exchange of Die).
Une démarche SMED consiste à réduire le temps écoulé entre la dernière pièce bonne produite au temps de cycle nominal et la première pièce bonne de la série suivante produite au temps de cycle nominal.
Le principe consiste à décomposer tous les temps entre ces deux repères de temps.
Dans les faits, il est pertinent de réaliser une analyse de déroulement en notant des éléments qui permettent de caractériser la tâche :
- Chronologie des tâches
- Effectif par tâche
- Temps par tâche
- Type de tâche (VA ou NVA)
- Si NVA, le type de gaspillage concerné
- Type de temps (interne ou externe)
- Type d’outillage utilisé
L’analyse, réalisée avec les personnes qui effectuent les réglages, permettra de mettre en évidence des problèmes de disponibilités des matériels qui peuvent générer des temps d’arrêts et des déplacements, des problèmes de séquençage des tâches, des problèmes liés au nombre d’outils nécessaires, etc.
Suivant les cas, les axes de réduction des temps seront d’ordre organisationnels comme faire préparer les nouveaux outillages avant l’arrêt de l’équipement ou d’ordre technique comme réduire la diversité du nombre de vis utilisées.
En premier lieu, on s’intéressera à convertir des temps dits internes en temps dits externes.
Les temps internes concernent toutes les opérations qui sont réalisées avec l’équipement à l’arrêt. Les temps externes sont tous les temps de préparation ou pré-réglages qui sont ou qui peuvent être réalisés sans nécessiter d’arrêter l’équipement, en temps masqué de la production.
La mise à jour des standards permettra d’acter la méthodologie validée avec les acteurs du terrain.
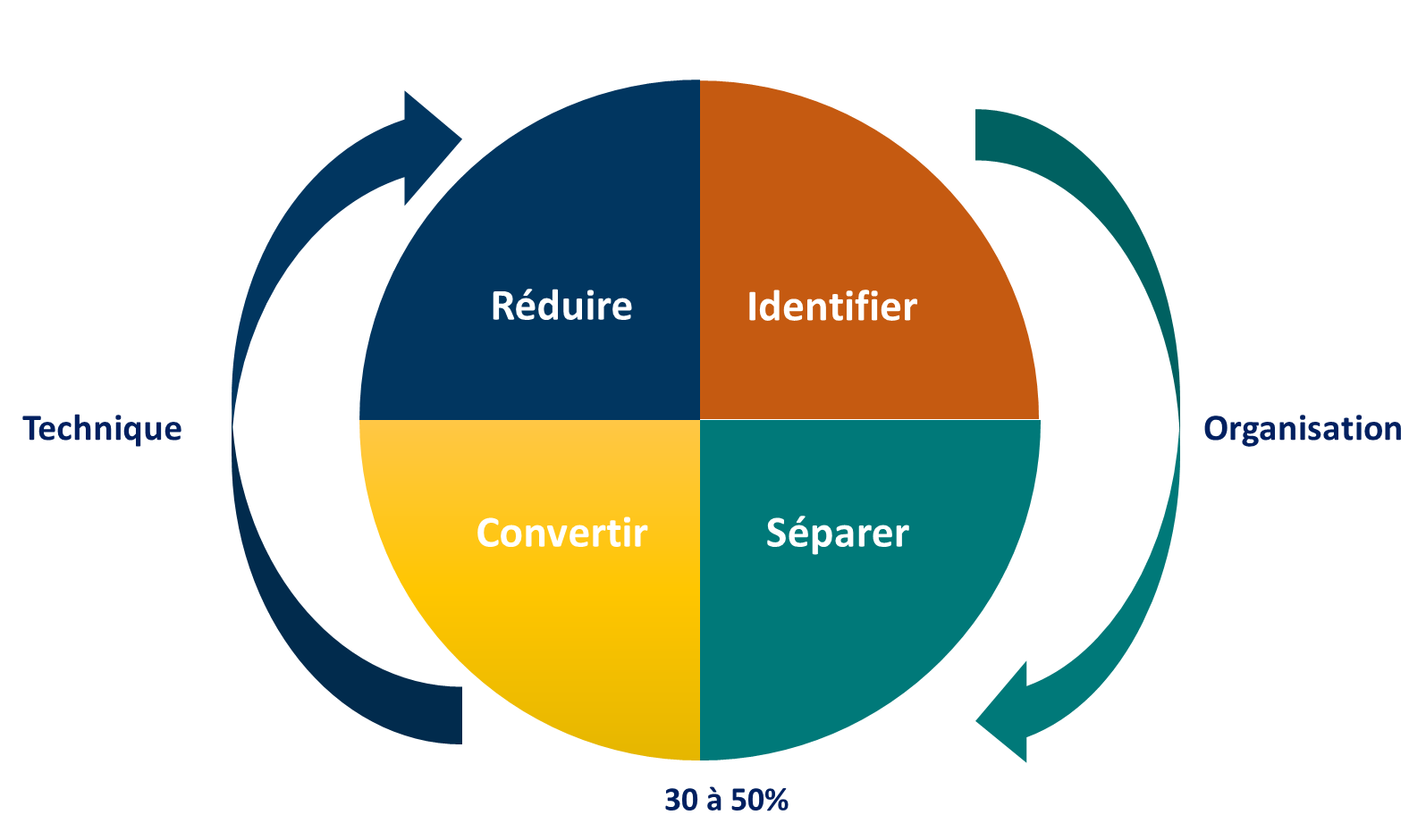
Voir notre article sur le SMED
3. Optimiser les flux physiques
S’intéresser aux flux physiques en identifiant les trajets effectués par les pièces, les outillages, les personnels permet d’identifier les gaspillages de temps et les risques associées aux déplacements.
Le diagramme spaghetti consiste à représenter graphiquement tous les flux physiques réels de l’organisation de production sur un plan de la zone de production concernée.
Quand le graphique est terminé, il est possible de quantifier les distances et les temps de déplacements mais aussi d’identifier les divers croisements qui rendent les flux complexes.
4. Maîtriser le bon fonctionnement des équipements avec la TPM
La maintenance globale des équipements (machines et outillages) par l’application des principes de la TPM (Total Productive Maintenance) est un gage de stabilité des processus.
La TPM est une démarche qui a pour but de maximiser l’efficacité des équipements par un processus complet, sur la totalité du cycle de vie des équipements. C’est une démarche basée sur des actions concrètes sur le terrain avec pour vocation la prévention des accidents, des défauts et des pannes.
La démarche TPM permet de coordonner tous les services qui conçoivent, entretiennent, utilisent et surveillent les équipements. En impliquant tout le monde, de la direction aux opérateurs.
La démarche TPM est animée sur la base d’un travail d’équipe et d’un objectif global de 0 pertes d’efficacité des équipements.
L’auto-maintenance se réfère aux actions conçues pour impliquer les opérateurs dans l’entretien de leur propre équipement, indépendamment du service maintenance.
Prendre soin de son poste, c’est le maintenir en état de bon fonctionnement.
Les activités typiques de la maintenance autonomes sont les suivantes :
- Inspection visuelle journalière
- Contrôle de bon fonctionnement des équipements (aspiration, arrosages, …)
- Opérations de graissage
- Opérations de contrôle et d’ajustement des niveaux
- Réparations simples (resserrages, réajustements)
- Identification des anomalies (micro fuites, bruits, température, vibrations…)
La TPM est pilotée par 3 indicateurs principaux :
> MTBF = Mean Time Before Failure
C’est le temps moyen de bon fonctionnement entre 2 pannes. Il mesure la fiabilité de l’équipement et l’efficacité des interventions.
> MTTR = Mean Time To Repair
C’est le temps moyen des interventions de réparation. Entre le moment où la machine est arrêtée et le moment où elle redémarre, pièces bonnes et à cadence nominale. Il mesure la réactivité du processus d’alerte et de remise en état de l’équipement.
> TRS = Taux de Rendement Synthétique
Le TRS est l’indicateur d’efficacité du processus de production. Pour la TPM il permet de mettre en évidence les pannes, les micro-arrêts, les diminutions de cadence.
5. Développer la polyvalence des collaborateurs
Le développement de la polyvalence permet de ne travailler que sur les postes concernés par la demande tout en maîtrisant le fonctionnement des équipements.
Avec l’aide des standards, l’accompagnement par des formateurs permet de valider les savoirs faire dans les différentes situations de production (réglages, changements d’outils, suivi production). Évaluer le niveau de savoir-faire permettra de déterminer le niveau d’autonomie au poste et donc le niveau d’accompagnement.
6. Déployer les standards
Merci pour votre lecture et rendez-vous début Janvier 2020 pour la quatrième partie de cette série d'articles sur les outils du Lean !