Lean Construction
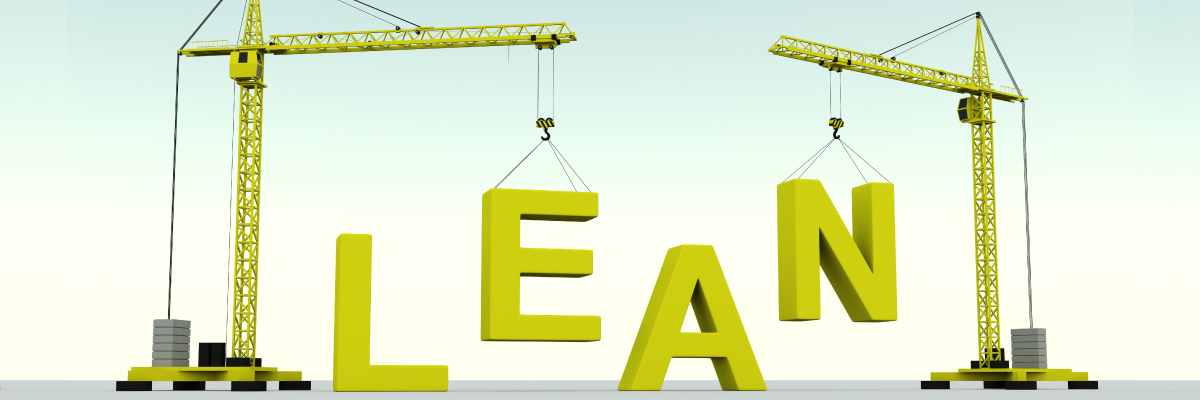
Cette fois c’est fait, les grands groupes du secteur de la construction ont entamé leur transformation vers des organisations plus agiles. Mais que de temps perdu ! En effet, si l’on reprend le fil de l’histoire du Lean, on retrouve des expériences très concluantes dans le milieu de la construction, menées par Franck Gilberth, dès 1890. Mais ensuite, plus rien jusqu’en 1993 où on reparle de Lean Construction avec la création du « International Group for Lean Construction » puis la création du LPS (Last Planner System). Pendant ce temps là, Toyota et son TPS (Toyota Production System), a popularisé la méthode. Mais de ce fait, le Lean a trop souvent été associé à l’industrie, à l’automobile, et de nombreux dirigeants se sont dit que ce n’était pas pour eux. Il faudra attendre ensuite 2010 pour voir apparaitre les premières publications en français sur le Lean Construction (Lean Construction, F Font et H Grua, édition Dunod).
Les enjeux dans le BTP
Quand on pose la question sur un chantier, rapidement cela tourne autour de la rentabilité et de la sécurité. Si la sécurité n’est pas discutable, la focalisation sur la rentabilité amène la plupart du temps à des effets pervers : extrême silotage des services qui défendent leur budget au détriment, parfois, de l’intérêt du chantier, compromis sur la qualité des prestataires et dispersion des énergies à se justifier plutôt que de trouver des solutions. Il est vrai que beaucoup de chantiers sont pris avec des marges très faibles (voir négatives) et que la motivation du coût est forte. Mais si pour une fois, on considérait cet enjeu comme une résultante d’autres axes de progrès ? Et si on réfléchissait dans le sens Sécurité, Qualité, Délai puis enfin Coût ?
Quels constats aujourd’hui ?
Les différents gaspillages provoquent inéluctablement un allongement des délais et donc du temps de traversée. Cela va faire baisser la performance de production et donc dégrader la valeur pour le client. De plus, la course contre le temps permanente sur les chantiers n’incite pas à prendre le recul nécessaire à la remise en cause des pratiques en place. Ce qui produit un cercle vicieux où on ne prend pas le « risque » de réfléchir et donc un certain fatalisme sur le fait que les problèmes font parties du métier !
Quelques chiffres :
- Un compagnon marche en moyenne 20% de son temps (7 à 10km/j) et un chef de chantier est interrompu en moyenne toutes les 6 mn
- Les coûts directs des non-conformités représentent 2 à 3% du CA
- 10% du CA est dépensé en reprises
- La première chose est de rendre visible les gaspillages par la mise en place d’un 5S avec les équipes de terrain.
- 30% des heures travaillées sont gaspillées
- 35% du délai chantier peut être évité
Par où commencer ?
Rentrer dans une démarche Lean est avant tout un chemin où l’on va réapprendre à tout le monte, à voir, pour résoudre les problèmes. Mais apprendre à voir quoi ?
La première chose est de rendre visible les gaspillages par la mise en place d’un 5S avec les équipes de terrain.
- L’attente (compagnon, grue, matériaux, …)
- Les stocks de matière
- Les reprises
- Les exécutions réalisées en avance
- Les tâches inutiles (Surqualité)
- Les gestes inutiles et l’ergonomie
- Les transports de matériaux
- Et enfin, le fait de ne pas utiliser les compétences des compagnons ou des chefs d’équipes dans l’amélioration de leur travail
Le 5S
La première chose est de rendre visible les gaspillages par la mise en place d’un 5S avec les équipes de terrain.
- Éliminer les choses inutiles ou cassées
- Ranger à proximité ce que l’on utilise souvent
- Nettoyer et supprimer les causes de salissure
- Formaliser la règle
- Respecter la règle et continuer de l’améliorer
Attention : le 5S n’est pas une session de nettoyage, mais bien un changement d’état d’esprit pour voir ensemble les écarts de rangement, les problèmes de sécurité, les manques de préparation…
La pyramide de management
C’est une étape fondamentale dans le processus d’Excellence Opérationnelle. C’est dans ces instances de pilotage de l’on va constater les écarts par rapport aux objectifs, anticiper les prochaines séquences et lancer les plans d’action.
Le briefing : Réalisé par le CE avec les compagnons, ce rituel quotidien permet de remonter les problèmes et organiser la journée.
Le J-1 : Réalisé par le Conducteur de travaux et le Chef de Chantier (ou CE), ce point permet de lever les derniers points bloquant pour le lendemain.
Le LPS (Last Planner System) Hebdo : C’est le moment charnière de la semaine, piloté par le Conducteur des Travaux où les différents intervenants du chantier et les corps d’état planifient ensemble les prochaines étapes et analysent les causes de non-respect des promesses faites la semaine précédente.
Le planning à 6 semaines : Réalisé par le Directeur des Travaux, le Conducteur des Travaux et les Sous-Traitants, c’est un point hebdomadaire où ils anticipent les prochaines étapes et s’assurent que les points bloquants sont levés (sécurité, main d’œuvre, informations, matériel, matériaux et tâches préalables) et les actions à mener.
La résolution de problème
Comme je l’ai dit plus haut, toute la démarche d’Excellence Opérationnelle sert à voir les problèmes. Mais une fois ceux-ci identifiés, il faut les résoudre de façon structurée afin d’éviter leur réapparition. Petit rappel : un problème est un écart entre ce qui est arrivé et ce qui était prévu. Encore faut-il que la notion de « prévu » soit expliquée, partagée et comprise par tous. Pour cela, il est indispensable d’avoir des standards. Évidemment, on ne va pas tout formaliser mais si vous avez des problèmes de bullage dans vos voiles, peut-être serait-il utile de standardiser les bonnes pratiques pour éviter l’intervention de l’équipe de finition…
Revenons sur la notion de méthode structurée de résolution de problème : c’est l’inverse des opérations pompiers dont nous sommes tous friands !
Pour cela, il faut se poser et réaliser les étapes suivantes :
- Définir le problème (QQOQCP) et mettre en place les actions correctives rapides (pompier)
- Mesurer et identifier les différentes causes possibles (collecte de données, plan de mesure)
- Analyser et trouver les causes profondes (5M, 5 Pourquoi)
- Mettre en œuvre les actions correctives
- Contrôler les résultats, formaliser par des standards
Conclusion
Le constat est qu’aujourd’hui, le Lean Construction s’est développé uniquement par le terrain et la mise en pratique de quelques outils dont ceux que je vous ai cité. Malheureusement, l’autre enjeu des groupes de construction, et pas des moindres, est la capitalisation des bonnes pratiques.
Chaque chantier est une entreprise, qui nait, qui souffre, qui apprend et qui disparait ! Comment pérenniser d’un chantier à l’autre avec des équipes qui se font et se défont au fil du temps ? Cela ne peut se faire que par le partage de standards et par la formation des compagnons et du management. La mise en place d’une culture n’est qu’à ce prix et pas par l’utilisation d’une boîte à outil.
De plus, une transformation en profondeur nécessite de l’accompagnement, et trop souvent les équipes Lean sont considérées comme des coûts et non pas comme des ressources qui peuvent accompagner durablement les chantiers vers la rentabilité.
Alors ? Et si vous essayiez une autre voie ?
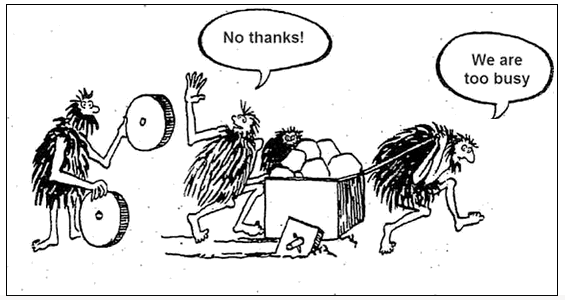