La TPM pour prendre soin de vos machines et vos clients
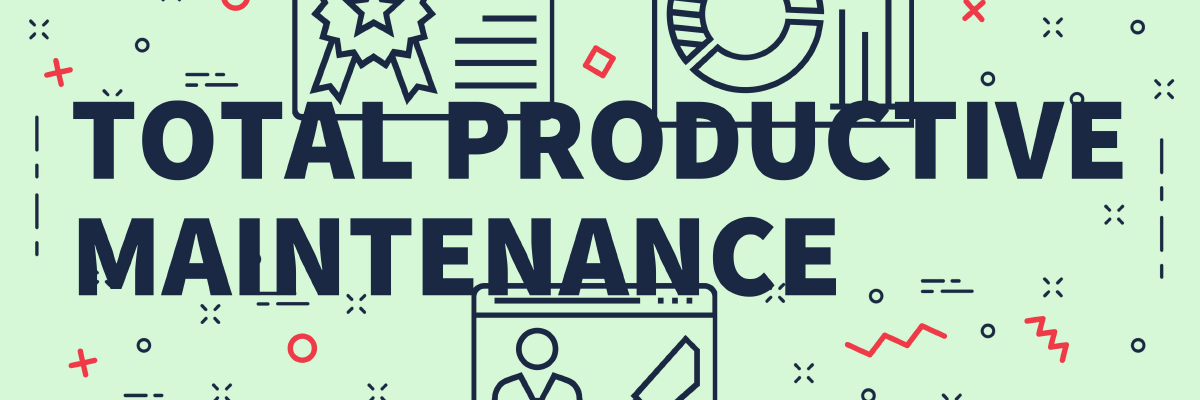
L’intérêt de la TPM dans une démarche Lean
La TPM (Total Productive Maintenance) est une démarche qui a pour but de maintenir les équipements dans des conditions optimales en impliquant toutes les fonctions de l’entreprise : Production, Maintenance, Ressources Humaines, Service Méthode…
C’est un système qui repose sur plusieurs piliers qui vont permettre de rendre les équipements plus fiables dans le temps :
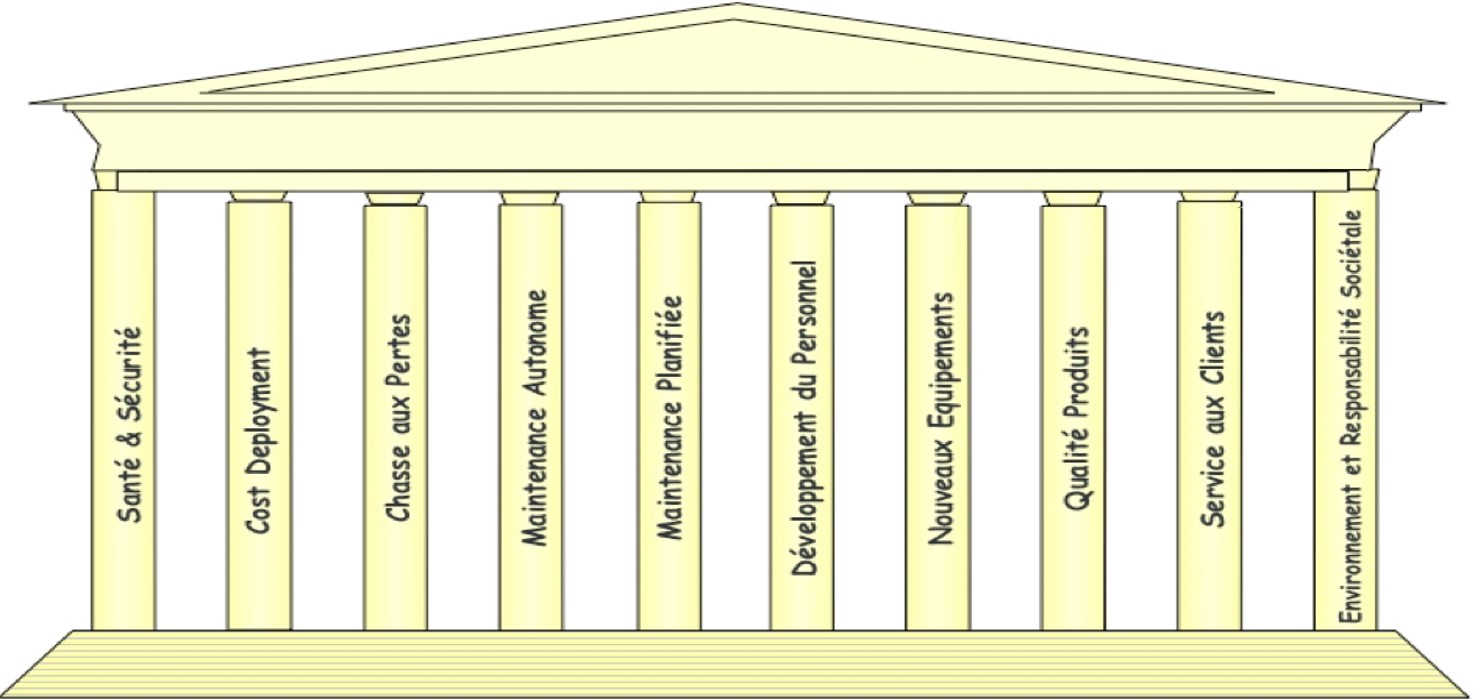
Photo 1 : La TPM est un système composé de piliers qui contribue à maintenir les équipements dans leur état optimal en utilisant toutes les compétences de l’entreprise
Source : https://worldclassmanufacturing.files.wordpress.com/2012/01/10-piliers.jpg
Dans une démarche Lean, nous sommes amenés à mettre en place la TPM lorsque nous identifions un équipement critique dans un flux de fabrication. C’est ce que nous appelons le « Goulot ».
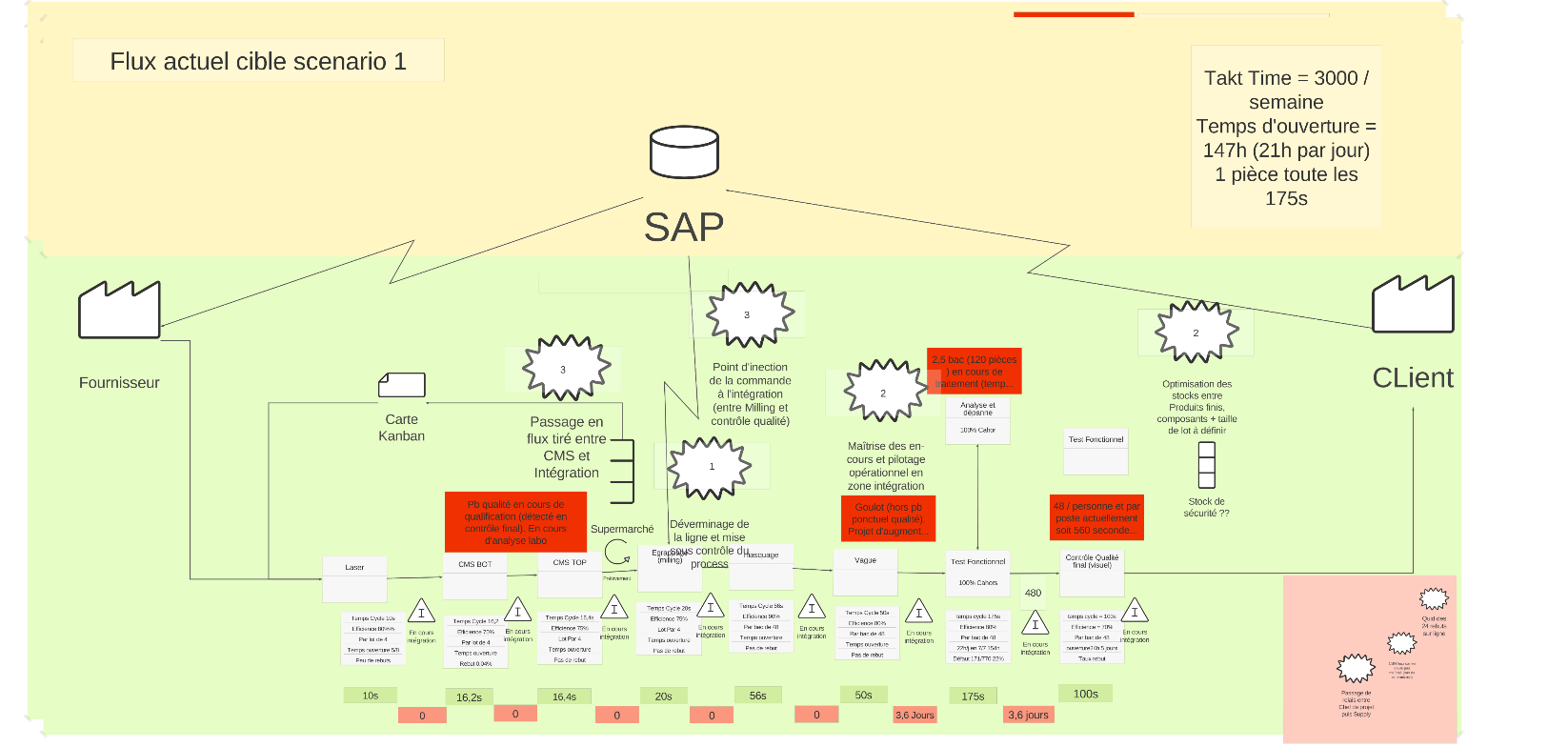
Photo 2 : Comprendre le flux de fabrication est fondamental dans une démarche Lean. La VSM (voir notre article sur la VSM) est l’outil fondamental pour identifier les équipements critiques qui rallongent le temps de défilement d’une commande en production
Lorsque le goulot est un équipement, il est nécessaire de mesurer sa performance pour connaître son état.
Mesurer la performance de l’équipement avec le TRS
Le premier réflexe lorsque l’on parle de performance d’un équipement est de mesurer son Taux de Rendement Synthétique (TRS), également nommé OEE en Anglais dans le texte (Overall Equipment Effectiveness).
C’est l’indicateur clé qui mesure donc la capacité d’une machine à créer de la valeur pendant son temps de fonctionnement (exprimé en %).
Cette mesure nous indique l’efficience de l’équipement ente 0% et 100%. Elle représente le pourcentage du temps passé à produire des pièces conformes par rapport au temps d’ouverture.
Principe de calcul du TRS :
Le rendement machine (TRS) exprime le rendement réel par rapport à l'idéal de fonctionnement
= temps ressource passé à créer de la valeur temps / total disponible
Objectifs :
- Mesurer la performance d’un moyen de production en caractérisant le niveau de bonne utilisation de la ressource
- Le TRS est un excellent outil d’investigation pour identifier les pertes en vue de visualiser et quantifier toutes les causes de NVA
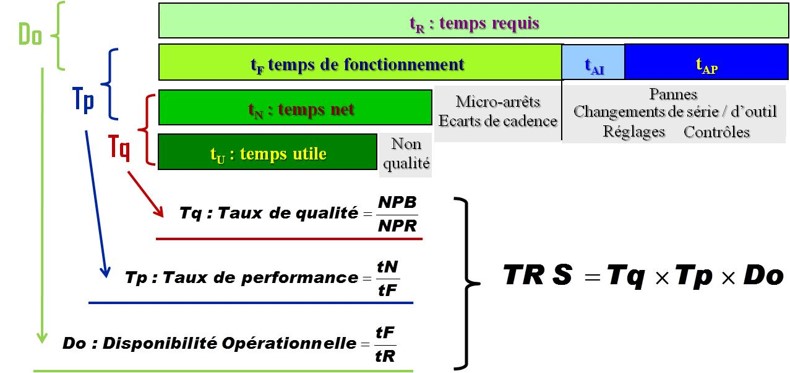
Photo 3 : Principe de calcul du TRS (Taux de Rendement Synthétique) d’un équipement
Et ce qui nous intéresse encore plus que le TRS dans du Lean, c’est le « Non TRS » : pourquoi nous ne sommes pas à 100% (les fameux gaspillages) ?
- Pièces rebutées ou retouchées
- Pannes
- Changements de série
- Ecart de cadence entre la cadence théorique et la cadence observée
- …
Maintenant que nous connaissons la performance actuelle de l’équipement et l’intérêt de la TPM, il va falloir mettre en place la TPM dans le bon ordre et montrer qu’il y a un réel intérêt pour la ou les équipements en question.
C’est pourquoi chez XL, nous démarrons nos missions par un diagnostic. Il nous permet d’évaluer le niveau de maturité du système de maintenance par rapport aux bonnes pratiques définies dans la TPM.
Attention, cela ne veut pas dire que tout est à déployer. Il faut mettre en place pas à pas en fonction des résultats observés et sélectionner ensemble les prochaines améliorations souhaitées sur la maintenance.
Une organisation trop souvent cloisonnée
En prenant le temps d’observer plus en détail les activités opérationnelles lors du diagnostic, nous faisons un constat malheureusement trop fréquent :
- Le service maintenance se focalise sur ses coûts de fonctionnement et de stock de pièces détachées et part du principe que les pannes sont principalement dues à une mauvaise utilisation de l’équipement.
- Le service production optimise ses ressources (la main d’œuvre et le TRS des équipements) en partant du principe que les pannes sont dues à une mauvaise maintenance.
L’objectif de prendre soin de la machine pour la rendre plus fiable n’est pas forcément partagé et la situation peut se dégrader sans aucune action mise en œuvre.
Il est donc souvent nécessaire de commencer par reclarifier les objectifs et les responsabilités de chaque acteur dans les activités de maintenance.
C’est ce que nous ferons notamment lors d’un chantier d’auto-maintenance que nous ciblons sur l’équipement en question.
L’auto-maintenance : Premier pas vers la TPM
La TPM a l’avantage de proposer des outils simples mais ils sont nombreux et peuvent être parfois lourds en termes de temps pour les opérationnels.
Il faut donc démarrer dans le bon ordre et progresser pas à pas. Ne chercher pas à tout faire en même temps (cela risquerait de décourager les parties prenantes et ce n’est pas Lean !).
Le but d’un chantier d’auto-maintenance va donc être de définir pour un équipement donné :
- La maintenance niveau 1 (celle réalisée par les personnes qui utilisent la machine)
- La maintenance niveau 2 et 3 (réalisée en général plus par le service maintenance voir par le fournisseur de la machine)
L'opérateur, qui est toujours à proximité de l'équipement, effectuera les inspections de base et de maintenance, pour assurer la conformité aux conditions de base et empêcher la détérioration accélérée.
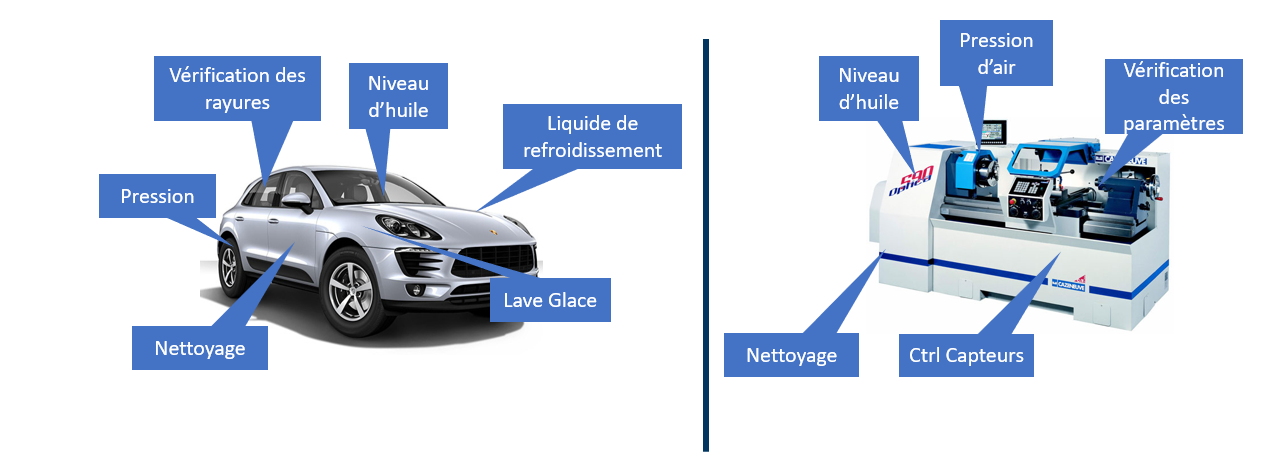
Photo 3 : L’objectif d’un chantier d’auto-maintenance est de définir la maintenance qui doit être réalisé par les différents acteurs par niveau de maintenance (niveau 1, 2 et 3)
Ceci aura pour avantage de clarifier et partager les bonnes conditions d’utilisation et de maintenance de la machine pour qu’elle dure et qu’elle soit plus fiable.
Un chantier d’auto-maintenance durera généralement entre 2 et 5 jours en fonction de l’équipement et impliquera l’ensemble des parties prenantes pour :
- Restaurer les conditions de bases de la machine en éliminant les anomalies
- (Re)construire des standards d’utilisation et de maintenance de l’équipement
Ces 2 éléments vont permettre d’améliorer rapidement le TRS de votre équipement, donc le flux de fabrication ainsi que la satisfaction de vos clients.
L’auto-maintenance sera également l’occasion de démontrer l’intérêt de la TPM pour votre entreprise !
Conclusion : De la TPM à un état d’esprit
Comme vous l’avez compris au travers de cet article, la TPM est un allié incontournable pour fiabiliser vos équipements.
Mais au-delà de la TPM, c’est bien une autre manière de travailler ensemble qui doit être amenée en faisant travailler ensemble les services de production, de maintenance, de planification et de méthodes industrielles pour :
- Choisir les bons équipements
- Planifier les opérations dans le bon ordre pour optimiser les temps de changement de série
- Réaliser la bonne maintenance préventive adaptée
- Conduire avec soin les machines
Les sujets seront nombreux et l’énergie de chacun sera primordiale pour atteindre vos objectifs !
Pour plus d’information sur la TPM et sur les démarches Lean, n’hésitez pas à nous contacter (formation, diagnostic et conduite de chantiers d’amélioration).