Compte-rendu de visite d’une usine Toyota
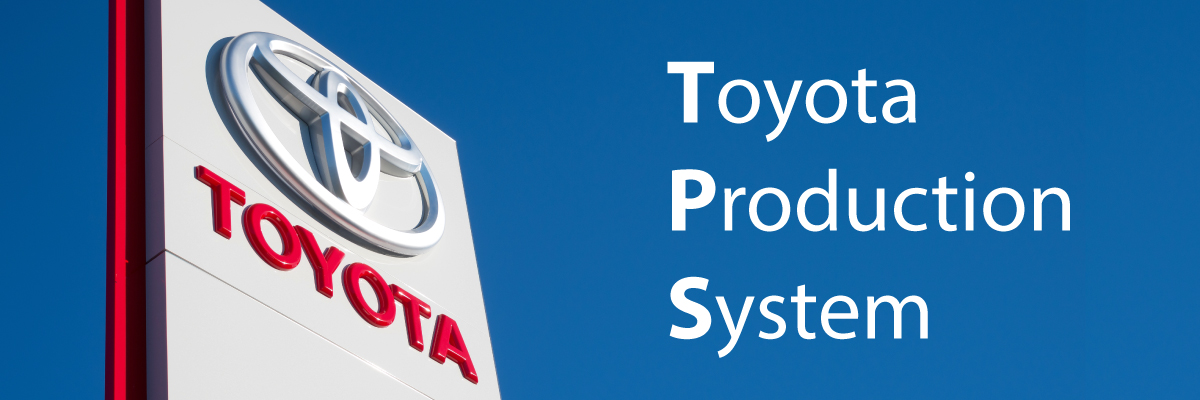
Il y a quelques années, j'ai eu la chance de visiter l'usine automobile située à KOLIN en Tchéquie. Cette usine est issue d'une joint-venture entre PSA et TOYOTA. Elle fabrique les Peugeot 107, Citroën C1, Toyota AYGO. J'ai pu alors découvrir concrètement ce que le LEAN veut dire, et plus particulièrement ce que représente le TPS (Toyota Production System) de façon très concrète.
Première impression : tout est blanc ! Murs, machines, mobiliers … Pour une usine de production automobile, notamment le ferrage (soudure) c'est très impressionnant. Cela permet à tous de voir les problèmes. Lorsqu’il y a une fuite ou une salissure, il est beaucoup plus efficace de traiter la cause que de la masquer.
Ensuite, ce qui m'a marqué, c'est la sérénité et la force qui se dégagent des opérateurs sur leur poste de travail. Pas d'affolement, pas de gens qui courent dans tous les sens. Une assurance de réussir sa journée en forte opposition avec l'agitation d'alors dans d’autres usines visitées. Chaque opération est clairement définie. Les nouveaux arrivants sont longuement formés dans une « école » avant d’être mis en poste. Pas de place à l‘improvisation et à la débrouille.
Et puis, en observant plus précisément les postes de travail, de nombreux points ont suscité mon étonnement.
Un premier exemple : les capots sont stockés différemment entre les trois modèles fabriqués. Deux sont stockés les uns par-dessus les autres, sans protection. Le troisième est stocké dans un conteneur particulier, bien séparé des deux autres modèles. J'interroge alors l'opérateur sur la raison d'un stockage différent. Un défaut d'aspect avait été constaté sur les capots. Un groupe de travail a été constitué avec des opérateurs de production. Après analyse, il s'est avéré que l'empilage d'un des capots posait problème, d'où le nouveau conteneur pour celui-ci. Pas besoin de modifier les autres conteneurs, puisque pas de défaut constaté. C'est le juste nécessaire pour assurer la Qualité de fabrication.
Autre exemple : sur la ligne de montage des ouvrants (portes, capots et volets), je m'aperçois qu'un poste est vide. En effet, pas de volet de coffre sur les C1, 107 et AYGO puisque c'est une vitre. Je m'étonne que le poste ait été conservé. La chaine de production aurait pu être raccourcie afin de gagner de la place et des investissements. Renseignement pris auprès de notre accompagnateur : Ce poste est prévu dans l'usine mère située au Japon. Afin que le standard d'usine soit respecté, le poste existe mais n'est pas utilisé.
Mon interlocuteur me donne alors une anecdote pour renforcer cette « toute-puissance » du standard. Lors de la conception de l’usine, les équipes PSA ont proposé de ne pas peindre l’intérieur des portes des véhicules. Cette pratique existait depuis longtemps chez PSA mais pas chez Toyota. Toyota a refusé malgré l’évident intérêt économique. L’usine a donc démarré en peignant l’intérieur des portes. Six mois plus tard, les équipes de développement Toyota sont revenues du Japon afin de supprimer cette fameuse opération. Etonnement des Français ! Pourquoi avoir attendu ? Les Japonais ont alors grandement remercié leurs homologues pour les économies réalisées sur l’ensemble des usines Toyota dans le monde ! Solution testée et approuvée en usine-mère et donc déployée industriellement sur l’ensemble du Groupe.
Un dernier exemple : sur la ligne de soudage de la caisse du véhicule, je remarque deux robots inactifs. Ce sont des robots « back-up » sur lesquels les équipes peuvent transférer des points de soudure pour pallier une panne d’un de leurs confrères. C’est une pratique courante sur ce type de ligne de production. Ce qui l’est moins, c’est que des simulations de panne sont planifiées tous les mois pour vérifier si ces marches dégradées sont opérationnelles et si le temps de mise en œuvre est respecté. Un standard doit toujours être accompagné de sa vérification afin de s’assurer de sa faisabilité dans le temps et/ou de trouver des améliorations.
En conclusion, s’il fallait définir le TPS (Toyota Production System), je dirais que c’est l’addition du GBS, du STD, de la VRS et de l’ACT.
Plus clairement, du Gros Bon Sens, du Standard, de la Vérification du dit Standard et de l’Amélioration Continue sur le Terrain !
Pour en savoir plus sur ce sujet, je vous invite à visionner le replay de la web-conférence « XL Groupe et le Toyota Production System » animée par Eric Huguerre et Cyril Bourgeon.